Innovative Recycling Strategy for Biodegradable Plastics: Closed-Loop Recycling from PLA to High-Performance Polymers
Abstract
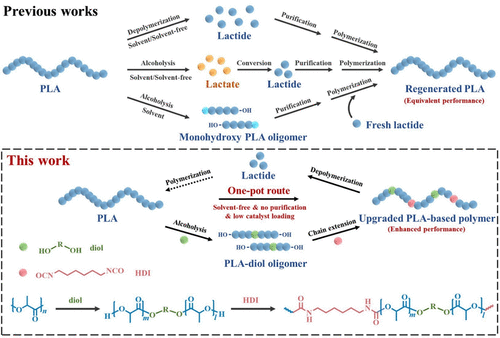
Traditional non-degradable plastics derived from fossil fuels have caused severe environmental pollution and resource wastage. In recent years, biodegradable plastics derived from renewable resources have gained increasing attention. Polylactic acid (PLA) is one of the most promising biopolymers due to its excellent biocompatibility, processability, and mechanical properties, making it widely used in disposable plastics, textiles, and food packaging. However, PLA can only degrade into H₂O and CO₂ in controlled industrial environments, and the process of converting its degradation products back into PLA is lengthy and involves multiple steps, such as crop growth, fermentation, and polymerization. Therefore, the recycling of waste PLA has been a major concern for both academia and industry.
Research Progress
Recently, a team led by Academician Wang Yuzhong and Professor Wu Gang from Sichuan University developed a simple solvent-free one-pot recycling strategy that effectively converts PLA and waste PLA disposable products into polymers with superior performance. This strategy involves controlled rapid catalytic alcoholysis to prepare hydroxyl-terminated PLA oligomers (PLA-diol), followed by chain extension reactions to produce PLA-based polyurethane (PLA-PU). PLA-PU exhibits better mechanical properties than PLA and can be processed through injection molding, melt spinning, and 3D printing. Moreover, PLA-PU can be directly depolymerized into the monomer L-lactide under vacuum conditions, demonstrating excellent recyclability and realizing the concept of closed-loop recycling from PLA to PLA-PU and back to PLA.
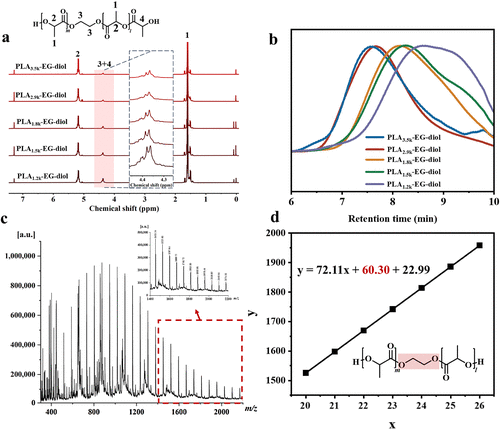
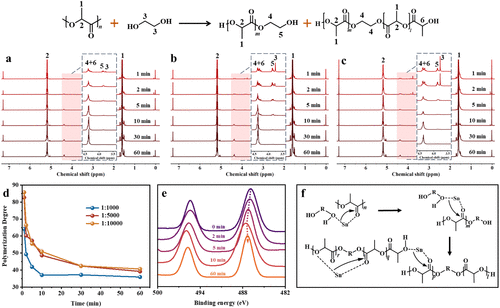
Methods and Results
Depolymerization Conditions Exploration:
The research team used ethylene glycol (EG) as the reactant and tin octoate as the catalyst to study the alcoholysis of PLA, with the optimal reaction temperature set at 190°C. Under different catalyst concentrations and reaction times, the PLA alcoholysis reaction proceeded rapidly within 10 minutes, reaching equilibrium in about 30 minutes. The study found that a molar ratio of catalyst to PLA repeating units of 1:10000 provided the highest reaction efficiency.
Characterization of PLA-EG-Diol:
Under optimal reaction conditions, by adjusting the molar ratio of EG to PLA, the team successfully synthesized hydroxyl-terminated PLA oligomers (PLA-EG-diol), with tunable molecular weight and structure.
Characterization of PLA-EG-PU:
Without separation and purification, the alcoholysis product was directly subjected to chain extension with HDI at 160°C, resulting in PLA-based polyurethane (PLA-EG-PU). The molecular weight of PLA-EG-PU could be adjusted by the structure of PLA-EG-diol, with yields as high as 97%-99%.
Performance of PLA-Based Polymers:
The study found that PLA-EG-PU exhibited good thermal stability and mechanical properties, with a glass transition temperature ranging from 42.0°C to 47.1°C, and significantly improved tensile strength and ductility.
Practical Application and Recyclability:
The research team validated the applicability of this solvent-free one-pot recycling strategy in actual waste PLA products and successfully achieved chemical closed-loop recycling from PLA to PLA-PU and back to PLA, with lactide monomer yield and purity both exceeding 90%.
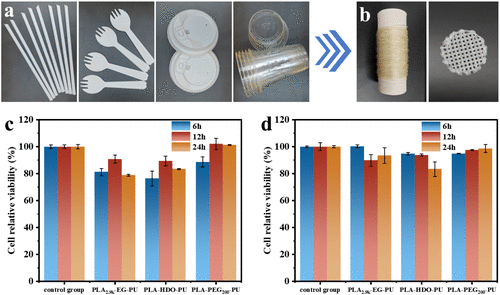
Conclusion
This study presents an efficient solvent-free one-pot strategy for the recycling and performance enhancement of PLA and its waste disposable products through alcoholysis and chain extension processes. Compared to conventional PLA, PLA-PU not only shows excellent mechanical properties but is also suitable for various processing methods and can be depolymerized into lactide after use, achieving closed-loop recycling. This work offers a potential new industrial pathway for the recycling of PLA and other aliphatic polyester plastics.
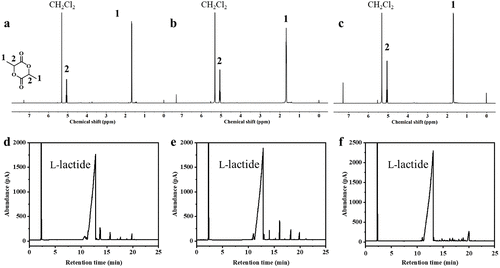
Reference
This work was published in the journal Macromolecules under the title "Solvent-Free One-Pot Recycling of Polylactide to Usable Polymers and Their Closed-Loop Recyclability."